9CM25C
The 9CM25C generator set brings to the offshore industry a legacy of proven reliability and durability in the marine industry. CM offshore generator sets feature standard modular designs, engine-mounted pumps and filters, and a full range of factory attachments that make their installation simple and efficient.Ideal applications for the 9CM25C offshore generator sets are main power on-board production vessels and platforms.Complete package offerings are MCS type-approved and compliant with IMO Tier II emissions standards, making their integration into vessels and platforms a simplified operation.Cat generator sets are backed by the worldwide network of Cat dealers ready to support your operation with technical support, service, parts, and warranty.Cat 9CM25C offshore generator set. Ratings: 2880 ekW (3600 kVA) @ 50/60 Hz (750/720 rpm). IMO Tier II emissions compliant.
engine specifications
Minimum Rating2880.0 ekW
Maximum Rating2880.0 ekW
EmissionsIMO Tier II
AspirationTurbocharged-Aftercooled
Engine ControlElectronic
Generator Set ControlElectronic
Weight56000.0 kg
Stroke400.0 mm
Bore255.0 mm
Displacement184.0 L
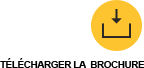
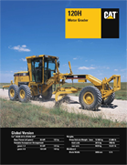
dimensions
Length9516.0 mm
Height4437.0 mm
Width2534.0 mm
capacity for liquids
Cooling System (Engine)900.0 L
Lube Oil System (Refill)3000.0 L
9CM25C STANDARD EQUIPMENT
- engine
– Motor-driven barring gear, fitted on engine
– Reversing contractor and pushbutton switch with cable
– Electronic speed setting equipment with actuator and speed pick-up
– Emergency shutdown equipment with pushbutton, separate, formanual emergency stop - engine indicators
– Gauge board with set liquid damped pressure gauges for:fuel, lubricating oil, fresh water, starting air, and charge air.
– On-engine thermometers for fuel, lubricating oil, fresh water,and charge air
– Electric remote speed indicator
– Turbocharger and remote speed indicator
– Exhaust gas temperature indicator - control
– Manual control on engine, including: control panel with start /stopkey, speed setting device, mechanical shutdown device, change overof control functions from engine to remote control
– Starting solenoid valve on engine, 24 V DC
– Separate electronic speed governor - monitoring for unattended operation
Pressure switches, mounted on engine, for:– Lube oil pressure at full load below danger level– Low lube oil pressure– Lube oil pressure below danger level– Lube oil pressure prelubrication failed– Low fresh water pressure at engine inlet– Fresh water pressure at engine inlet below danger level– Low fresh water pressure in LT circuit– Low starting air pressure– Low control air pressure engine/shutdown air pressure– Low fuel pressure at engine inletSwitches for:– High lube oil temperature at engine inlet– Lube oil temperature at engine inlet above danger level– High water temperature at engine inlet– Water temperature at engine outlet above danger level– High charge-air temperature at engine inlet– Detection of water in charge-air duct– Leak fuel level– Alarm contact for high differential pressure at fuel filter– Alarm contact for high differential pressure at lube oil backflushing filter– Set of thermocouples after each cylinder, before and afterturbocharger– Crankcase oil mist detectorControl Cabinet with housings for wall mounting, including:– Protection equipment designed for automatic and manual stop inputsignals, starting interlock input signals, monitoring for the wire breakof the input signal units and the emergency shutdown solenoid– Speed recording system for overspeed, firing speed and minimumspeed– Start /stop logic, controlled by engine automatic start (optional)– Service hour counter– Noris alarm system, cassette type, designed for alarm inputs for theengine including exhaust mean-value monitoring equipment as wellas alarm inputs for the propulsion plant– Group alarm panel for the bridge and with optional andacoustical alarm equipment - starting air system
– Separate non-return valve for the starting air pipe to the engine - air intake system
– Air intake filter, fitted on the turbocharger
– Air bottles, separate - diesel oil system
– Separate circulating pump driven by electric motor, horizontalor vertical
– Duplex filter with differential pressure indication - exhaust system
– Turbocharger at free end with transition nozzle (0 degrees from thevertical and away from engine), with compressor cleaning device
– Expansion joint separate
– Separate silencer and spark arrester, unlagged 35 dB(A) - fresh cooling water system
– HT pump, fitted on engine
– LT pump, separate, vertical design, electric motor driven
– HT thermostat, not powered and separate
– Engine preheating equipment, fitted on base frame - lubricating oil system
– Plate cooler, fitted on engine
– Force pump, fitted on engine
– Prelubrication pump, fitted on base frame, electric motor driven
– Boll and Kirch automatic backflushing filter, separate
– Duplex filter with differential pressure indication, separate
– Pressure control valve, separate
– Thermostat, not powered, separate - connecting parts engine
– Set of connecting parts between flange coupling and flywheel
– Flexible flange coupling between engine and generator
– Base frame with flywheel guard and incorporating lube oil sump tank,for engine and generator
– Mounting of engine and generator on the base frame
– Set of bonded rubber rails for resilient mounting of the base frame
– Set of flexible pipe connections - tools
– Set of tools for turbocharger
– Set of tools for turbocharger
– Inside micrometer for cylinder liners
– Ruler for cylinder liner - spare parts
– Set of engine spare parts for unrestricted operation
– Set of spare flexible pipe connections