EL2000 - SHEARER
The EL2000 incorporates all the features and benefits that have been established with the Cat shearer range in a compact, rugged machine designed to meet the demands of high productivity in low- to medium-seam applications from 1.80 to 4.50 m (70 to 177 in.). High installed power is a feature of the EL2000 shearer, with up to 750 kW (1,200 hp) in a compact design. The haulage system is tailored to the needs of high-productivity medium-seam applications with up to 125 kW (200 hp) AC drives.
SPECIFICATIONS
Typical Machine Length14.1 m
Installed Power1780.0 kW
Haulage SystemAC inverter drive
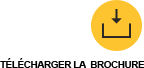
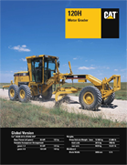
BENEFITS AND FEATURES
shear performance
With high-powered ranging arms and haulage units, Cat shearers cut and load up to 5000 ...
LEARN MOREkey improvements
Cat shearers incorporate numerous new features and benefits. These are presented in the ...
LEARN MOREmainframe made for muscle
The unique mainframe of the Cat shearer is one of its key features. The fabricated ...
LEARN MOREspecifications
Typical Machine Length14.1 m
Installed Power1780.0 kW
Haulage SystemAC inverter drive
Applicable Minimum Pan Width1032.0 mm
Available Cutting Power2 × 500 kW; 2 × 620 kW; 2 × 750 kW
Available Haulage Motors2 × 125 kW (2 × 168 hp)
Body Height600.0 mm
Cutting Drum Diameter1600-2500 mm (63-98.5 in)
Haulage PullUp to 945 kN (Up to 107 tons)
Haulage SpeedUp to 30.1 m/min (Up to 98.5 ft/min)
Height Range1.80-4.50 m (71-177 in)
Machine WeightApprox. 70 tonnes (Approx. 77 tons)
Operating Voltages3300V; 4160V
Pump Motor30.0 kW
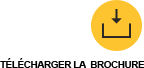
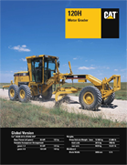
electrical control box ecb2
TypeThis flameproof module contains the majority of the shearer electrical control and power distribution components.
TypeHigh current carrying capacity of 400 amps and can accommodate trailing cables up to 185 mm2 (2.9 in2).
TypeAll internal chassis can be ‘bench built,’ tested and stored.
TypeThis unit also contains high voltage (HV) fuses, earth leakage and a visible disconnect.
TypeAn extremely powerful PMC Evo-S control system with state-of-the-art Ethernet communication and backup functionality.
TypeThis unit contains cutter motor contactors, circuit breakers, control transformer and current monitoring.
TypeBox contains various low voltage (LV) circuit breakers which can be reset through the flame proof (FLP) cover, reducing downtime
health monitoring
TypeThis system monitors oil levels and temperatures, flows, pressures and vibration.
TypeA comprehensive health monitoring system is available.
dimensions approximate midlow
AFC Pan Width - Maximum1342.0 mm
AFC Pan Width - Minimum1032.0 mm
Clearance from Drum to AFC Toeplate300.0 mm
Cutting Heights - Maximum4135.0 mm
Cutting Heights - Minimum1900.0 mm
Diameter of Shearer Cutting Drum1900.0 mm
Distance between Drums with Arms Horizontal14155.0 mm
Distance between Ranging Arm Hinge Points8525.0 mm
Distance between Trapping Shoe Centers6056.0 mm
Height to Top of Machine Main Body1495.0 mm
Machine Height over Main Body1495.0 mm
Maximum Cutting Drum Overall Width1150.0 mm
Ranging Arm Cutting Drum Diameter1900.0 mm
Ranging Arm Length (Hinge to Drum)2815.0 mm
Shearer Drum Undercut of Floor718.0 mm
Vertical Tunnel Clearance649.0 mm
machine @ 50 hz
Available Cutting Power2 x 500 kW (2 x 671 hp); 2 x 620 kW (2 x 831 hp); 2 x 750 kW (2 x 1,006 hp)
Body Height600.0 mm
Cutting Drum Diameter1600-2500 mm (63-98.5 in)
Cutting Drum Speed32.8, 37.4 and 45.2 rpm
Haulage Motor2 x 125 kW (2 x 168 hp)
Haulage PullUp to 945 kN (96 tons)
Haulage SpeedUp to 30.1 m/min (98.8 ft/min)
Haulage SystemAC inverter drive
Installed PowerUp to 1780 kW (Up to 2,387 hp)
Machine Weight (approximate)70.0 tonnes
Minimum Pan Width1032.0 mm
Operating Voltage3300.0 volts
Pump Motor30.0 kW
Seam Range1.8-4.5 m (71-177 in)
Typical Machine Length (drum centers)14155.0 mm
water material
TypeAll hose assemblies are to ISO 6805 and proof tested to EN ISO 1402.
TypeThis shearer is available with onboard filtration, dust suppression spray bars, shearer clearers and ranging arm spray rings.
TypeThe hoses are assembled to Hose Assembly Standard DIN20066:201-10.
haulage unit hu125
Maximum Machine Speed28.56 m/min
Pull at Maximum Speed472.75 kN/106,278 lbf (48.40 tonnes/53.35 tons)
Speed at Maximum Pull14.28 m/min
Total Machine Pull945.51 kN/212,559 lbf (96.80 tonnes/106.70 tons)
TypeQuillshaft transmission protection
TypeIntegral water cooling @ 9 L/min (2 gal/min)
TypeIntegral monitoring transducers
TypeMaximum oil capacity of 25 L (7 gal)
TypeTransmission reduction of 137:1
TypeMaximum power rating 125 kW (168 hp)
TypeThis unit has a haulage motor rating of 125 kW (168 hp)
ranging arm ra750
TypeTransmission rating of 750 kW @ 37.4 rpm and above
TypeMaximum drum diameter of 2500 mm (98 in)
TypeSquare drum hub (440 mm [17.3 in] across flats)
TypeA robust cowl drive mechanism is also available on this model
TypeOnline vibration monitoring with VibraGuard
TypeAvailable cutter motors - 500 kW, 620 kW and 750 kW, @ 50 Hz (800 hp, 1,000 hp and 1,200 hp, @ 60 Hz)
TypeChoice of drum speeds
TypeComplete with 32 mm (1.3 in) bore, through shaft PFF/PBF wet cutting
TypeIntegral monitoring transducers
TypeQuillshaft transmission protection
TypeMaximum oil capacity of 28 L (7 gal) in high speed compartment and 30 L (8 gal) in the epicyclic
machine automation and communication
Levels of AutomationState-based shearer automation “Navigator 2”
Levels of AutomationZone-based automation “Navigator 1”
Levels of Automation“Longwall Navigator” for improved face alignment and horizon control
Levels of AutomationIntegrated longwall automation with “Navigator 2 + 3”
TypePMC Evo-S control system allows the shearer to be operated even if the overall control system is not functioning.
TypeThe shearer is equipped with a state-of-the-art industry PC in a flame-proof housing with plenty of computing power.
TypeState-of-the-art industry PC allows flexibility to upgrade to future features such as condition monitoring.
TypeUnlike competitor systems, modularity of the longwall system
control allows the longwall to operate in “faulttolerant” mode
Machine Automation and CommunicationType
in other words integrated automation does not prevent control via individual plc’s in order to keep production up and running
Machine Automation and CommunicationType
pmc evos control system with stateoftheart ethernet communication and backup functionality
Machine Automation and CommunicationType
this shearer has a stateoftheart distributed automation system for the control monitoring and protection of the shearer
Machine Automation and CommunicationType
a programmable logic controller plc takes care of basic machine control tasks ensuring that coal is produced
Machine Automation and CommunicationType
industryleading automation from the pioneer of statebased automation
Machine Automation and CommunicationType
its modular design allows it to be configured to meet individual control needs
Downdrive - DD125Type
suitable for all current rack type systems
Downdrive - DD125Type
transmission rating of 125 kw 168 hp
Downdrive - DD125Type
maximum haulage pull 945 kn 107 tons
Downdrive - DD125Type
innovative and unique downdrive design
Downdrive - DD125Type
removable modular top drive wheel assembly cartridge
Downdrive - DD125Type
downdrive ratio 17t—23t—10t two wheel configuration
Downdrive - DD125Type
trapping shoe with replaceable wear inserts safe and easy to replace unique to caterpillar
Downdrive - DD125Type
fully removable rehandable modular gearbox
Haulage Transformer Box - HTB2Type
module contains drive system circuit breaker and one 250 kw 600v ac inverter drive with regenerative braking module
Haulage Transformer Box - HTB2Type
this flameproof module contains the main 253 kva haulage transformer power supplies and auxiliary transformer
Electrical MaterialType
this model of shearer is available with headlights cameras methane monitoring end displays and audible alarms
Electrical MaterialType
all electrical material is designed and certified to iec standards and also complies with other regional and national standards
Dimensions (Approximate) - LowAFC Pan Width - Maximum
13420 mm
Dimensions (Approximate) - LowAFC Pan Width - Minimum
10320 mm
Dimensions (Approximate) - LowClearance from Drum to AFC Toeplate
3000 mm
Dimensions (Approximate) - LowCutting Heights - Maximum
39300 mm
Dimensions (Approximate) - LowCutting Heights - Minimum
18000 mm
Dimensions (Approximate) - LowDiameter of Shearer Cutting Drum
16000 mm
Dimensions (Approximate) - LowDistance between Drums with Arms Horizontal
141550 mm
Dimensions (Approximate) - LowDistance between Ranging Arm Hinge Points
85250 mm
Dimensions (Approximate) - LowDistance between Trapping Shoe Centers
64530 mm
Dimensions (Approximate) - LowHeight to Top of Machine Main Body
14440 mm
Dimensions (Approximate) - LowMachine Height over Main Body
Dimensions (Approximate) - LowMaximum Cutting Drum Overall Width
11500 mm
Dimensions (Approximate) - LowRanging Arm Cutting Drum Diameter
16000 mm
Dimensions (Approximate) - LowRanging Arm Length (Hinge to Drum)
28150 mm
Dimensions (Approximate) - LowShearer Drum Undercut of Floor
6190 mm
Dimensions (Approximate) - LowVertical Tunnel Clearance
5980 mm
Dimensions (Approximate) - Mid-HighAFC Pan Width - Maximum
13420 mm
Dimensions (Approximate) - Mid-HighAFC Pan Width - Minimum
10320 mm
Dimensions (Approximate) - Mid-HighClearance from Drum to AFC Toeplate
3000 mm
Dimensions (Approximate) - Mid-HighCutting Heights - Maximum
43600 mm
Dimensions (Approximate) - Mid-HighCutting Heights - Minimum
22000 mm
Dimensions (Approximate) - Mid-HighDiameter of Shearer Cutting Drum
Dimensions (Approximate) - Mid-HighDistance between Drums with Arms Horizontal
141550 mm
Dimensions (Approximate) - Mid-HighDistance between Ranging Arm Hinge Points
85250 mm
Dimensions (Approximate) - Mid-HighDistance between Trapping Shoe Centers
66120 mm
Dimensions (Approximate) - Mid-HighHeight to Top of Machine Main Body
15710 mm
Dimensions (Approximate) - Mid-HighMachine Height over Main Body
Dimensions (Approximate) - Mid-HighMaximum Cutting Drum Overall Width
11500 mm
Dimensions (Approximate) - Mid-HighRanging Arm Cutting Drum Diameter
22000 mm
Dimensions (Approximate) - Mid-HighRanging Arm Length (Hinge to Drum)
28150 mm
Dimensions (Approximate) - Mid-HighShearer Drum Undercut of Floor
7930 mm
Dimensions (Approximate) - Mid-HighVertical Tunnel Clearance
7250 mm
Powerpack - PP2Type
operating system pressure of 260 bar 3770 psi
Powerpack - PP2Type
integral monitoring transducers
Powerpack - PP2Type
for use with iso 68 or iso 100 hydraulic oils
Powerpack - PP2Type
robust hydraulic reservoir of 165 l 436 gal capacity
Powerpack - PP2Type
this unit has a pump motor rating of 30 kw @ 50 hz 48 hp @ 60 hz
Powerpack - PP2Type
fixed displacement pump with a capacity of 50 lmin 1321 galmin
Powerpack - PP2Type
available with 6 section valve bank
Hydraulic MaterialType
all hose and hosing is in compliance with guideline mdg 41 and msha regulations
Hydraulic MaterialType
the hoses are assembled to hose assembly standard din2006620110
Hydraulic MaterialType
all hose assemblies are to iso 6805 and proof tested to en iso 1402
OptionsType
available with machine parking brake
OptionsType
available with machine position encoder
Mainframe - MF2Type
maximum protection of electrical boxes providing the highest level of flameproof integrity
Mainframe - MF2Type
improved access for maintenance and ease of overhaul and repair
Mainframe - MF2Type
versatility of application due to fully modular construction
Mainframe - MF2Type
high structural integrity and absorption of all cutting and haulage forces providing maximum protection for all major units
Mainframe - MF2Type
a split mainframe is available in case of transportation limitations
Dimensions (Approximate) - HighAFC Pan Width - Maximum
13420 mm
Dimensions (Approximate) - HighAFC Pan Width - Minimum
10320 mm
Dimensions (Approximate) - HighClearance from Drum to AFC Toeplate
3000 mm
Dimensions (Approximate) - HighCutting Heights - Maximum
45700 mm
Dimensions (Approximate) - HighCutting Heights - Minimum
25000 mm
Dimensions (Approximate) - HighDiameter of Shearer Cutting Drum
Dimensions (Approximate) - HighDistance between Drums with Arms Horizontal
141550 mm
Dimensions (Approximate) - HighDistance between Ranging Arm Hinge Points
85250 mm
Dimensions (Approximate) - HighDistance between Trapping Shoe Centers
60560 mm
Dimensions (Approximate) - HighHeight to Top of Machine Main Body
16470 mm
Dimensions (Approximate) - HighMachine Height over Main Body
Dimensions (Approximate) - HighMaximum Cutting Drum Overall Width
11500 mm
Dimensions (Approximate) - HighRanging Arm Cutting Drum Diameter
25000 mm
Dimensions (Approximate) - HighRanging Arm Length (Hinge to Drum)
28150 mm
Dimensions (Approximate) - HighShearer Drum Undercut of Floor
8660 mm
Dimensions (Approximate) - HighVertical Tunnel Clearance
8010 mm
Machine @ 60 HzAvailable Cutting Power
2 x 597 kw 2 x 800 hp 2 x 746 kw 2 x 1000 hp 2 x 895 kw 2 x 1200 hp
Machine @ 60 HzBody Height
6000 mm
Machine @ 60 HzCutting Drum Diameter
16002500 mm 63985 in
Machine @ 60 HzCutting Drum Speed
394 449 and 543 rpm
Machine @ 60 HzHaulage Motor
2 x 125 kw 2 x 168 hp
Machine @ 60 HzHaulage Pull
up to 1049 kn 107 tons
Machine @ 60 HzHaulage Speed
up to 30 mmin 985 ftmin
Machine @ 60 HzHaulage System
ac inverter drive
Machine @ 60 HzInstalled Power
up to 1780 kw up to 2387 hp
Machine @ 60 HzMachine Weight (approximate)
780 tonnes
Machine @ 60 HzMinimum Pan Width
10320 mm
Machine @ 60 HzOperating Voltage
41600 volts
Machine @ 60 HzPump Motor
300 kw
Machine @ 60 HzSeam Range
1845 m 71177 in
Machine @ 60 HzTypical Machine Length (drum centers)
140820 mm
BENEFITS AND FEATURES
SHEAR PERFORMANCE
With high-powered ranging arms and haulage units, Cat shearers cut and load up to 5000 ...
LEARN MOREKEY IMPROVEMENTS
Cat shearers incorporate numerous new features and benefits. These are presented in the ...
LEARN MOREMAINFRAME MADE FOR MUSCLE...
The unique mainframe of the Cat shearer is one of its key features. The fabricated ...
LEARN MOREINNOVATIVE TRAPPING SHOE
Trapping shoes attach the shearer to the haulage rack system, part of the armored face ...
LEARN MOREEXTENDED SERVICE LIFE
The inserts have the same wear area as conventional shoes and are articulated.
LEARN MOREDOWNDRIVE
An innovative downdrive design results in longer bearing life, increased gear rating and ...
LEARN MOREMODULAR HAULAGE SYSTEM
Caterpillar has further developed its modular haulage concept with increased power ...
LEARN MORECOALSIZER
Cat shearers can be supplied with an optional rugged coalsizer, currently with up to 200 ...
LEARN MOREPACKING MORE POWER
The power pack has been reengineered to provide increased functionality, optimized ...
LEARN MORETESTED FOR RELIABILITY
Downtime is extremely expensive for operators - costs continue to add up while nothing is ...
LEARN MORELUBRICATION VERIFICATION
Ranging arms and haulage units are subjected to an intense test regime to establish the ...
LEARN MOREENDURANCE BLOCK LOAD TESTING
This test applies loads far in excess of those encountered during normal mining ...
LEARN MOREPRODUCTION LOAD TESTING
After successful endurance block load testing, the same test rigs are used to carry out ...
LEARN MOREPROVEN PRODUCTIVITY
This extensive range of tests ensures the highest possible availability of shearers in ...
LEARN MOREINDUSTRY-LEADING AUTOMATION ...
Caterpillar has developed a state-of-the-art distributed automation system for the ...
LEARN MOREPOWER AND FLEXIBILITY
With extensive computer power installed and simple upgrade to new features, Cat shearer ...
LEARN MORETHE NET IS THE CONTROL
The shearer control system uses a state-of-the-art Ethernet bus, resulting in a drastic ...
LEARN MOREINTRINSIC SAFETY
More components designed to be intrinsically safe means simpler installation and speedier ...
LEARN MOREVISUALIZATION
Visualization not only provides a graphical representation of current operating ...
LEARN MOREVIBRAGUARD™
VibraGuard™ allows trained personnel to predict machine component wear, avoid unplanned ...
LEARN MOREMODULAR CONTROL OFFERS ...
PMC™ Evo-S brings state-of-the art processor performance underground. Designed by the ...
LEARN MOREEL2000 STANDARD EQUIPMENT
- trapping shoe ix
- central lubrication system
- pmc™ evos
- gate end data connection
Powerline
WLAN
EL2000 OPTIONS
- multipiece mainframe
- cowl
- spall guards
- coal sizer
100 kW - trapping shoe ix insert exchange
- shearer clearer
- spray bars
- ipc
- zonebased automation“navigator 1”
- statebased shearer automation “navigator 2”
- integrated longwall automation with “navigator 2 + 3” only with cat longwall equipment
- “longwall navigator” for improved face alignment and horizon control incorporates lasc technology only with cat longwall equipment
- vibraguard™
- cameras
- condition monitoring
MOTEUR
With high-powered ranging arms and haulage units, Cat shearers cut and load up to 5000 tonnes (5,500 tons) per hour and more, depending on mining conditions. The unique, one-piece mainframe design offers maximum structural integrity and service life.
BENEFITS AND FEATURES
The mainframe is available as a split unit in the event of transportation limitations. Featuring the superior Jumbotrack shearer haulage system, the shearer also offers advanced integrated automation and communication options.
Cat shearers incorporate numerous new features and benefits. These are presented in the following pages by category.
BENEFITS AND FEATURES
The key improvements include:
- Extremely powerful PMC™ Evo-S control system with state-of-the-art Ethernet communication
- Improved innovative downdrive design
- Ranging arm with longer service life
- Further development of the modular haulage and electrical control box
- Enhanced power pack with easy access
- Online vibration monitoring with VibraGuard™
- Clear wiring and use of plug and play for easy maintenance
- Trapping Shoe Ix (Insert Exchange) for longer service life, safe and easy to replace
- Future-proof design allowing upgrades - such as stronger ranging arms and haulage units or addition of coal sizer - during rebuild
- Mainframe designed to handle 1200 kW (1,930 hp) ranging arms and 200 kW (320 hp) haulage units - EL3000 only
The unique mainframe of the Cat shearer is one of its key features. The fabricated structure of the mainframe with cast ranging-arm hinge points results in an extremely robust design not only to meet the toughest mining conditions and ensure reliability and long service life, but also to handle even higher cutting and haulage forces in the future. The mainframe of the EL3000 is designed to allow retrofit of 1200 kW (1,930 hp) ranging arms and 200 kW (320 hp) haulage units. A split mainframe is available in case of transportation limitations.
BENEFITS AND FEATURES
Benefits
- High structural integrity and absorption of all cutting and haulage forces, providing maximum protection for all major units
- Maximum protection of electrical boxes, providing the highest level of flameproof integrity
- Improved access for maintenance and ease of overhaul and repair
- Versatility of application due to fully modular construction
- Flexible and cost-effective equipment management
- Independent unit exchange and selective overhaul
- Long service life
- Low operational costs
- High reliability
Trapping shoes attach the shearer to the haulage rack system, part of the armored face conveyor, allowing the shearer to be hauled up and down the face.
BENEFITS AND FEATURES
A new type of trapping shoe developed by Caterpillar - the Trapping Shoe Ix - offers numerous advantages over the conventional design:
- Greater safety and ease of handling during replacement
- Faster replacement
- Greater flexibility
- Longer service life
- Lower operating costs
The inserts have the same wear area as conventional shoes and are articulated.
BENEFITS AND FEATURES
This - combined with the fact that the shoe does not have to exert as much pressure, resulting in a lower point load - means less wear. Field tests of the Trapping Shoe Ix showed its service life to be 50 percent longer than conventional trapping shoes.
An innovative downdrive design results in longer bearing life, increased gear rating and greater modularity for simplified maintenance. Height adjustment of the shearer is relatively easy and is achieved with replacement of the downdrive to allow adaption to changing seam conditions.
BENEFITS AND FEATURES
Every mainframe is designed to take the full range of downdrive arrangements to fit a wide range of seam heights.
- Fully modular design
- Easy maintenance access
- Fully articulating shoe
- High pull and maximum life
Caterpillar has further developed its modular haulage concept with increased power rating, gear rating, bearing life and redundancy, leading to longer overhaul intervals based on typical usage. The haulage system is a simple design capable of achieving cutting speeds of up to 32 m/min (105 ft/min), with improved reliability and longer service life.
BENEFITS AND FEATURES
The fully modular haulage gearbox is located in the shearer mainframe and does not form part of the shearer structure. The haulage system offers:
- Simple construction, improved reliability and longer service life
- Fully proven load-sharing system
- Reduced cost
Cat shearers can be supplied with an optional rugged coalsizer, currently with up to 200 kW (320 hp) of installed power for maximum productivity in high seams or difficult mining conditions.
BENEFITS AND FEATURES
The coalsizer can be ordered separately for installation during rebuild or overhaul.
The power pack has been reengineered to provide increased functionality, optimized performance and better access to filtration units via simplified layout. Both of the following units are modular, with drawer units providing easy access and upgrade.
BENEFITS AND FEATURES
Features Transformer Box
- Features closed-loop control with measurement of speed, not power
- Transforms to 600 V for haulage units’ frequency converter motors
- Connectorized cables for reduced wiring and quick, clear installation
- Temperature monitoring and water cooling
Control Box
- Plug and play
- Easy to maintain
- Quick and easy troubleshooting
Downtime is extremely expensive for operators - costs continue to add up while nothing is produced. This is why Caterpillar ensures that our superbly engineered shearers are up to the job.
BENEFITS AND FEATURES
That’s why each shearer design - which is optimized for maximum availability - is subjected to rigorous in-house testing to ensure that there are no unpleasant surprises when units are in service. Shearer production quality assurance falls into three main categories: lubrication verification, endurance block load testing and production load testing.
Ranging arms and haulage units are subjected to an intense test regime to establish the optimum oil-level requirements to suit all mining conditions. The units are mounted on purpose-designed test rigs that are positioned to simulate the gradient of the underground seam.
BENEFITS AND FEATURES
A suite of tests is performed with a range of different gradients and arm positions to represent even the most severe mining conditions. The units are operated until stable temperatures are achieved at all gradients. This establishes the minimum, maximum and optimum oil quantities for all conditions.
This test applies loads far in excess of those encountered during normal mining operations, ensuring that the shearer can operate reliably at the installed power ratings. Ranging arms or haulage units are mounted on purpose-designed test rigs in a back-to-back configuration driven by a suitable test motor.
BENEFITS AND FEATURES
The endurance block load test imposes loads from 100% to 175% to ensure that the ranging arm design meets the requirements of the most demanding applications. Input torque, losses and output torque are monitored during the test, as are bearing, gear and shaft temperatures. Vibration is monitored by dedicated sensors. Oil samples are collected at intervals for analysis, as the presence of metal in the oil can indicate excessive component wear. On completion of the endurance test, units are dismantled for a full internal and external inspection to verify that the design is fit for purpose.
After successful endurance block load testing, the same test rigs are used to carry out production load testing of all ranging arms and haulage units.
BENEFITS AND FEATURES
The test gradually increases the load up to full load. All temperatures and vibration points are monitored during the test, and oil samples are again collected for analysis.
This extensive range of tests ensures the highest possible availability of shearers in service and maximum return on investment for your longwall installation.
BENEFITS AND FEATURES
Nothing is left to chance in ensuring that our shearers are unsurpassed in reliability.
Caterpillar has developed a state-of-the-art distributed automation system for the control, monitoring and protection of the shearer. Its modular design allows it to be configured to meet individual control needs, from basic monitoring and protection to advanced automation and data transmission.
BENEFITS AND FEATURES
The PMC™ Evo-S control system with state-of-the-art Ethernet communication and backup functionality allows the shearer to be operated even if the overall control system is not functioning. In 2002, State-Based Automation was invented and launched. Using this technology, Caterpillar now offers a comprehensive range of automation products.
With extensive computer power installed and simple upgrade to new features, Cat shearer automation is fit for the future. Components connect into the network rather than directly to a central computer, simplifying installation, wiring, maintenance and troubleshooting.
BENEFITS AND FEATURES
The shearer is equipped with a state-of-the-art industry PC in a flame-proof housing with plenty of computing power, allowing flexibility to upgrade to future features such as condition monitoring. A Programmable Logic Controller (PLC) takes care of basic machine control tasks, ensuring that coal is mined. Unlike competitor systems, the modularity of the longwall system and control allow the longwall to operate in “fault-tolerant” mode, even when there is a problem with the overall automation system. In other words, integrated automation does not prevent control via individual PLCs in order to keep production up and running.
The shearer control system uses a state-of-the-art Ethernet bus, resulting in a drastic reduction in wiring and a huge increase in flexibility. There are no interfacing problems, as equipment connected to the network only needs to be able to communicate via Internet Protocol.
BENEFITS AND FEATURES
Commissioning, maintenance, upgrades and troubleshooting are much easier and faster, and equipment is self-configuring. The few cables that are used are standard Ethernet cables rather than application-specific cables - cutting costs and simplifying spare parts inventories. Flameproof housings are no longer required, simplifying installation and speeding up maintenance. New modules are based on standardized CIOS™ modules (configurable input output system), resulting in a plug and play approach to upgrades. No reprogramming is necessary. Remote control and diagnosis are also possible for all components. And because of the Ethernet-based approach, the failure of one component does not impact the whole system.
More components designed to be intrinsically safe means simpler installation and speedier maintenance. New modules are based on standardized CIOS™ modules, resulting in a plug and play approach to upgrades.
BENEFITS AND FEATURES
Changes to the system only require commissioning changes - such as mounting and connection of sensors. No replacement of control software is required. Remote control and diagnosis are also possible for all components. And because of the Ethernet-based approach, the failure of one component does not impact the whole system. This not only supports the unique “fault-tolerant” mode, which allows the longwall to continue to operate when there is a problem with the overall automation system, but also, through systematic isolation, allows faulty units to be identified while production continues.
Visualization not only provides a graphical representation of current operating conditions, but can also display historical conditions and a graphic display of trends. An automated longwall is a highly complex system with many interacting components generating time-variant data.
BENEFITS AND FEATURES
Visualization gives operators a better understanding of the overall system, allowing them to further optimize operations. VLongwall provides a system overview and access to the dedicated visualization modules VShield, VDrive, VPlow and VShearer. It also gives access to VTrend for trend analysis and VGraph3D for waterfall plots of the entire longwall.
VibraGuard™ allows trained personnel to predict machine component wear, avoid unplanned downtime and set alarms to warn the operator if monitored machine components run the risk of damage. This comprehensive protection backs long life and high availability of your valuable mining equipment.
BENEFITS AND FEATURES
Benefits
- Permanent online monitoring and protection of equipment instead of sporadic offline measurements
- Assists in the prediction of machine component wear
- Alarms warn the operator if monitored components are at risk of damage
- When utilized by trained personnel, VibraGuard™ makes repairs predictable and helps avoid unplanned downtime
- Repair work can be done largely without stress
- Allows timely procurement of spare parts
- Transfers data to a surface control center PC for detailed analysis and evaluation
PMC™ Evo-S brings state-of-the art processor performance underground. Designed by the market leader in shearer automation, the advanced Cat automation package allows improved utilization of manpower in a safe environment; with increased yield from any given seam section, faster haulage speeds, improved face management and increased life of all longwall equipment, including AFC and shields.
BENEFITS AND FEATURES
Automation systems match your needs - from basic to highly sophisticated - while remaining easy to install, operate and maintain. The modular control concept is:
- Easily expandable based on modular design
- Ready for integration of highly sophisticated technologies and devices
- Equipped for XML-based interfaces to third- or fourth-party systems
Making it Easy
- Cat self-configuring controls and standard interfaces such as Ethernet allow quick and easy system configuration changes with no programming effort
- Ready for future technologies such as high-quality condition monitoring, including vibration monitoring
- Easy and flexible adaptation to existing data environments
- Greater use of Ethernet, standard connectorization and PMC™ control family mean greater simplicity, reduced spares inventories and shorter downtimes
- Standardization and modularization allow quick and easy customization of components and systems
Fast Troubleshooting
- Widespread use of intrinsically safe components allows large-scale fault diagnosis under power
- Remote access to most components down to I/O level
- Diagnosis from surface or by Cat Mine Control Center
- Managed switches and field bus coupler (FBC) allows selective routing:
Less Maintenance Effort
- Widespread use of intrinsically safe components in PMC™ Evo-S reduces time-consuming opening of flame-proof housings in the event of faults.
- Quick and easy exchange of modules.
Modularity is Strength Modularity is a key feature of the Cat shearer. It results in independent major units, each driven by its own dedicated electric motor and housed within or attached to a robust mainframe unique to the Cat range. Control systems are also modular. This modular design offers maximum availability - through “fault-tolerant” mode operation - and the flexibility to meet even the most demanding customer requirements by upgrading components such as the ranging arm.