963D TRACK LOADER
Increased horsepower, excellent maneuverability, redesigned operator cab for comfort, the revolutionary SystemOne™ undercarriage and the new implement system increase your productivity, drastically reduce your operating costs and make the new 963D unsurpassed in versatility.
SPECIFICATIONS
Flywheel Power141.0 kW
Engine ModelCat® C6.6 ACERT™
Net Power - Cat141.0 kW
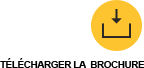
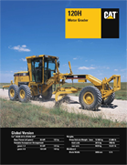
BENEFITS AND FEATURES
engine
Provides power, reliability and acts as a working counterweight in the rear of the ...
LEARN MOREoperator station
Designed for operator comfort, convenience, and ease of operation throughout the workday.
LEARN MOREmonitoring system
The gauge cluster provides all necessary functions and information within the ...
LEARN MOREengine
Flywheel Power141.0 kW
Engine ModelCat® C6.6 ACERT™
Net Power - Cat141.0 kW
Net Power - ISO 9249141.0 kW
Net Power - SAE J1349141.0 kW
Net Power - EEC 80/1269141.0 kW
Bore105.0 mm
Stroke127.0 mm
Displacement6.6 L
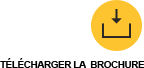
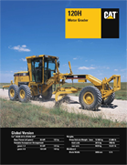
weights
Operating Weight20220.0 kg
buckets
Capacity - General Purpose2.45 m3
Capacity - Multi-Purpose2.0 m3
Bucket Width - General Purpose2612.0 mm
Bucket Width - Multi-Purpose2575.0 mm
undercarriage
Track Shoe TypeDouble Grouser
Track Shoe Width - Standard550.0 mm
Track Shoe Width - Optional450.0 mm
Track Rollers - Each Side7
Number of Shoes - Each Side38
Track on Ground2543.0 mm
Ground Contact Area - Standard Shoe2.8 m2
Ground Contact Area - Optional Shoe2.3 m2
Ground Pressure - Standard Shoe71.5 kPa
Ground Pressure - Optional Shoe85.5 kPa
Grouser Height - Double Grouser42.0 mm
Track Gauge1850.0 mm
drive system
Track MotorTwo, variable displacement, bent axis motors
hydraulic system equipment
TypeClosed center, load sensing / piston
Output209.0 L/min
Main Relief Valve Setting28000.0 kPa
service refill capacities
Fuel Tank400.0 L
Cooling System31.5 L
Crankcase (with Filter)16.5 L
Final Drives (each)15.0 L
Hydraulic Tank90.0 L
Pivot Shaft1.8 L
ripper specifications
TypeRadial
Number of pockets3
Overall Width/Beam1950.0 mm
Shank cross section58.5 mm x 138 mm 50 in x 5.4 in
Ground Clearance874.0 mm
Penetration271.0 mm
Ripping Width1836.0 mm
Cylinders - Bore114.3 mm
Cylinders - Stroke289.0 mm
Addition to Machine Length due to Ripper (in Transportation Position)494.0 mm
standards
ROPS/FOPSROPS/FOPS
BrakesBrakes
CabCab
bucket cycle times
Cycle Time - Dump1.3 Seconds
Cycle Time - Float Down2.9 Seconds
Cycle Time - Raise5.8 Seconds
Cycle Time - Total6.4 Seconds
BENEFITS AND FEATURES
ENGINE
Provides power, reliability and acts as a working counterweight in the rear of the ...
LEARN MOREOPERATOR STATION
Designed for operator comfort, convenience, and ease of operation throughout the workday.
LEARN MOREMONITORING SYSTEM
The gauge cluster provides all necessary functions and information within the ...
LEARN MORESYSTEMONE™ UNDERCARRIAGE
The SystemOne undercarriage was designed exclusively for Caterpillar machines to reduce ...
LEARN MORESPECIAL APPLICATION ...
Special arrangements improve the 963D’s performance in special applications.
LEARN MORESERVICEABILITY AND CUSTOMER ...
Grouped service points and excellent accessibility make the 963D easy to maintain.
LEARN MORE963D STANDARD EQUIPMENT
- electrical
Alternator, 24 volt, heavy duty brushless.
Alarm, backup
Horn, electric
2 heavy duty batteries, high output, maintenance free, 1120 CCA.
Switch, main disconnect
Starter, electric (heavy duty, 24 volt)
Four halogen lights, two forward facing, roof mounted; two rearward facing, integrated in A/C unit - operator environment
Pressurized, sound suppressed, ROPS/FOPS cab
Cab, windows, glued
Air conditioning and heater/ defroster with temperature control
Seat, fabric- covered, air suspended, adjustable, with side- to- side isolator
Seat belt, retractable
Electro Hydraulic Seat mounted control levers
Transmission control, V-lever
Control, joystick, bucket gp
Electronic Monitoring System with gauges for: •Engine coolant temperature •Hydraulic oil temperature •Engine oil pressure •Fuel level
Mirror, rearview, inside
Radio- ready. Includes 24 to 12 volt converter, speakers, antenna and 12 volt power outlet
12 volt outlets (2)
Coat hook
Storage compartments under left armrest
Document holder on right console
Floor mat, rubber, heavy duty
Windshield washers and wipers, front and rear
Durable metal roof
Parking brake switch and "brake- on" indicator light - powertrain
Caterpillar C6.6 ACERT engine diesel engine, turbo charged with ATAAC
Modular cooling system for engine air intake, oil and water
Fan radiator, electronically controlled, hydraulically driven, temperature sensing, on demand
Electro Hydrostatic Control (EHC) for transmission with travel and work modes
Fuel priming pump, electric
Water separator
Air inlet
Air cleaner dry- type, axial seal with integral pre- cleaner and dust ejection system, electronic filter condition indicator
Muffler, under hood
Starting aid ether injection
Caterpillar extended life coolant
Fuel, tank - undercarriage
Caterpillar SystemOne track (38 sec.) 72.8 In/ 1850 mm track gauge
Final drive, standard
Track, 550mm (21.6in), double grouser
Track adjuster, hydraulic
Sprocket rims, with replaceable bolt- on segments
7 single flange track rollers per side, with two upper carrier rollers, lifetime lubricated
Conventional idlers, lifetime lubricated
Idler, scrapper
Oscillating track roller frames - hydraulic
Oil change, standard
Hydraulic oil
Hydraulic, 2 way valve - guards
Guard, front
Guard, rear
Guards, full bottom - other standard equipment
Cab, tilt, locking bar
Sound Suppression, Exterior
Z- bar loader linkage
Load sensing variable displacement implement pump
Implement cylinders with integrated positioning sensors
Operator programmable lift and tilt kickouts
Engine enclosure with lockable doors
Radiator core 6.5fpi, debris resistant
Hinged Radiator Guard and swing out fan
Ecology grains on hydraulic tank
Product Link ready
Oil sampling valves
Hydraulic hoses, Caterpillar® XT
Hydraulic Oil, HYDO Advanced 10 - warning decals
Warning decals, ANSI, for NACD
Warning decals, ISO - service instructions
English Instructions included in North America and Canada only.
963D OPTIONS
- electrical
Beacon, rotating
Lights, four, extra - implement controls
Control, joystick, GP bucket
Control, joystick, MP bucket
Control, two levers, GP bucket - operator environment
Cat® Messenger
Seat, air suspended, heated
Cab windows, front sealed - powertrain
Fan, demand, reversing
Tank fuel, fast fill
Air inlet, pre-cleaner, turbine
Oil change, high speed - undercarriage
Track, 450 mm (17.7"), DG, narrow
Track, 550 mm (21.6"), DG, center hole
Track, 450 mm (17.7"), DG, center hole
Track, 560 mm (22"), SG, extreme service
Track, 450 mm (17.7") center hole, SG, extreme service
Track, 800 mm (31.5"), DG, wide gauge
Track, 560 mm (22"), center hole, SG, extreme service
Idler, with seal protection - guards
Guard, idler
Guard, track roller
Guard, cab lights
Guard, lift lines
Screen, windshield - hydraulic
Hydraulic oil, bio
Hydraulic, MP bucket, lines front
Hydraulic, ripper, lines rear
Hydraulic, MP bucket - ripper lines front
rear - bucket
General purpose
General purpose, flush mounted adapter
General purpose, landfill
Multi purpose
Multi purpose, extreme service
Multi purpose, landfill
Refuse - bucket attachments
Cutting edge, bolt- on
Segments, bolt- on
Edge, segments, bolt- on
Edge, segments, heavy duty
Teeth, general duty, K80
Teeth, penetration, K80
Teeth, extra duty, K80
Teeth, general duty, K90
Teeth, extra duty, K90
Tips, general duty, flush adapter - other attachments
Cab tilt jack, hydraulic
Bumper
Ripper, multi-shank
Hitch, drawbar
Hitch, standard
Striker bars, rear
Sediment pump, fuel tank
Heater, engine coolant, 120V
Heater, engine coolant, 240V
Counterweight, light
Counterweight additional
Caterpillar product link 321
Antifreeze, -50C (-58F) - guards
Guard front heavy duty
Lines GP- brake- M
Lines GP- Brake- Wide Gauge
MOTEUR
Provides power, reliability and acts as a working counterweight in the rear of the machine, for optimum machine balance.
BENEFITS AND FEATURES
Cooling module architecture The cooling system is a single cooling unit, which includes Radiator, ATAAC, Oil cooler and Fan installation. The cooling module is located at the rear of the loader, away from dust and debris stirred up by the bucket while the machine is working. The radiator has 6.5 fins per inch (fpi) which helps reduce plugging.
Cat C6.6 ACERT™ The Cat® C6.6 is a 6.6 liter (403 in3) displacement, six-cylinder, in-line configured engine that utilizes the Caterpillar Common Rail fuel system for fuel delivery. It uses ACERT™ Technology, a series of Caterpillar engineered innovations that provide advanced electronic control, precision fuel delivery and refined air management, resulting in outstanding performance and lower emissions. The C6.6 with ACERT Technology offers a compact design with big, heavy-duty engine features for outstanding durability, reliability and performance. The C6.6 incorporates a new cross flow cylinder head design, 4 valve head and an ADEM™ A4 electronic controller. The C6.6 also features proven cylinder block, pistons and crankshaft and incorporates the common rail fuel system. ACERT™ technology enables the C6.6 engine to meet the U.S. EPA Tier 3, European Union Stage IIIa and Japan Ministry of Land, Infrastructure
Electronic control. ADEM™ A4
BENEFITS AND FEATURES
16879790 Fuel System
16879790 Air Management
16879790 Fuel pump
16879790 Fuel Priming Pump
16879790 Starting System
16879790 Air-to-Air After cooler (ATAAC)
16879790 Servicability
16879790 Engine Installation
16879790 Rear Engine Location
16879790 Hydraulic on-demand fan
16879833 Operator Station
16879833 Storage spaces
16879833 Viewing Area
16879833 Kickout settings
16879833 Armrests
16879833 Heating and Air Conditioning
16879833 Caterpillar Air-suspension Seat
16879833 Seat mounted controls
16879833 Messenger
16879833 Hydrostatic Drive System Controls
16879833 Speed Switches
16879833 Electro-hydraulic implements controls
16879833 Rearview Mirror
16879833 Dome Light
16879833 Radio Installation Arrangement
16879833 Door release lever
16879833 Machine Security System
16879863 Monitoring System
16879863 Alert indicators
16879863 Gage cluster-self test.
16879804 Hydrostatic Drive
16879804
16879804 Electronic Hydrostatic Control (EHC)
16879804 Variable Displacement Pumps and Drive Motors
16879804 Travel Speeds
16879804 Speed-Direction Control Lever (SDL)
16879804 Braking
16879804 Steering
16879804 Maneuverability
16879867 Implement System
16879867 Electro-hydraulic Implement Controls
16879867 Load sensing hydraulics
16879867 Automatic kick-outs
16879867 Position sensing cylinder
Working lights
BENEFITS AND FEATURES
The 963D gauge cluster display
BENEFITS AND FEATURES
16879851
BENEFITS AND FEATURES
16879851
BENEFITS AND FEATURES
16879851
BENEFITS AND FEATURES
16879851
BENEFITS AND FEATURES
16879851
BENEFITS AND FEATURES
16879851
BENEFITS AND FEATURES
16879851
BENEFITS AND FEATURES
16879851
BENEFITS AND FEATURES
16879851
BENEFITS AND FEATURES
16879851
BENEFITS AND FEATURES
16879851
BENEFITS AND FEATURES
16879851
BENEFITS AND FEATURES
16879782
BENEFITS AND FEATURES
16879782
BENEFITS AND FEATURES
16879782
BENEFITS AND FEATURES
16879782
BENEFITS AND FEATURES
16879782
BENEFITS AND FEATURES
16879782
BENEFITS AND FEATURES
16879782
BENEFITS AND FEATURES
16879782
BENEFITS AND FEATURES
16879813
BENEFITS AND FEATURES
16879813
BENEFITS AND FEATURES
16879813
BENEFITS AND FEATURES
16879813
BENEFITS AND FEATURES
16879813
BENEFITS AND FEATURES
16879813
BENEFITS AND FEATURES
16879764
BENEFITS AND FEATURES
16879764
BENEFITS AND FEATURES
16879764
BENEFITS AND FEATURES
16879764
BENEFITS AND FEATURES
16879764
BENEFITS AND FEATURES
16879764
BENEFITS AND FEATURES
16879764
BENEFITS AND FEATURES
16879764
BENEFITS AND FEATURES
16879764
BENEFITS AND FEATURES
16879764
BENEFITS AND FEATURES
16879819
BENEFITS AND FEATURES
16879819
BENEFITS AND FEATURES
16879819