120K MOTOR GRADER
The K Series Motor Grader is the machine you can count on when you need to get work done. Cat motor graders help you make the most of your investment by delivering maximum productivity and durability. The Cat C7 engine, direct-drive power shift transmission and load sensing hydraulics work together to ensure the power and precision you need to work in demanding conditions. And Cat motor graders are backed by the world-class Cat dealer network to keep you up and running.
SPECIFICATIONS
Base Power (1st gear) - Net93.0 kW
Engine ModelCat® C7 ACERT™
VHP - gears 1-2 Net93.0 kW
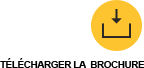
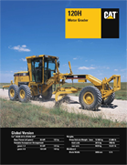
BENEFITS AND FEATURES
engine
Base Power (1st gear) - Net93.0 kW
Engine ModelCat® C7 ACERT™
VHP - gears 1-2 Net93.0 kW
VHP - gear 3 Net101.0 kW
VHP - gears 4-8 Net108.0 kW
VHP - gears 1-2 Gross103.0 kW
VHP - gear 3 Gross110.0 kW
VHP - gears 4-8 Gross118.0 kW
Displacement7.2 L
Bore105.0 mm
Stroke127.0 mm
Speed @ rated power2000.0 RPM
Number of cylinders6
Derating altitude3048.0 m
High Ambient Capability50.0 ° C
VHP Range - Net93-108 kW (125-145 hp)
Base Power (1st gear) - Net (Metric)93.0 kW
Fan Speed Maximum1575.0 RPM
Maximum Torque Net774.0 N·m
Torque Rise50.0 %
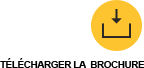
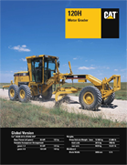
weights
Gross Vehicle Weight - Typically Equipped13843.0 kg
Gross Vehicle Weight: Base - total12133.0 kg
Gross Vehicle Weight: Maximum - total17000.0 kg
Gross Vehicle Weight: Typically Equipped - front axle3970.0 kg
Gross Vehicle Weight: Typically Equipped - rear axle9873.0 kg
Gross Vehicle Weight: Typically Equipped - total13843.0 kg
Gross Vehicle Weight: Base - front axle3120.0 kg
Gross Vehicle Weight: Base - rear axle9013.0 kg
Gross Vehicle Weight: Maximum - front axle5197.0 kg
Gross Vehicle Weight: Maximum - rear axle11803.0 kg
moldboard
Blade Width3.7 m
Moldboard - height610.0 mm
Moldboard - thickness22.0 mm
Arc Radius413.0 mm
Throat Clearance58.0 mm
Cutting Edge - width152.0 mm
Cutting Edge - thickness16.0 mm
End Bit - width152.0 mm
End Bit - thickness16.0 mm
Blade Pull - maximum GVW10623.0 kg
Down Pressure - maximum GVW9317.0 kg
Blade Pull - base GVW8112.0 kg
Down Pressure - base GVW5594.0 kg
weights typically equipped
Operating Weight - Typically Equipped30519.0 kg
Gross Vehicle Weight13843.0 kg
power train
Forward/Reverse Gears8 forward/6 reverse
TransmissionDirect drive, Powershift
Brakes - ServiceAir actuated, multiple oil-disc
Brakes - Service, surface area18606.0 cm2
Brakes - ParkingAir actuated, multiple oil-disc
Brakes - SecondaryDual Circuit
operating specifications
Top Speed - forward47.5 km/h
Top Speed - reverse37.5 km/h
Turning Radius, outside front tires7.3 m
Steering Range - left/right47.5 Degrees
Articulation Angle - left/right20.0 Degrees
Forward - 1st4.1 km/h
Forward - 2nd5.5 km/h
Forward - 3rd8.0 km/h
Forward - 4th11.1 km/h
Forward - 5th17.5 km/h
Forward - 6th23.7 km/h
Forward - 7th32.7 km/h
Forward - 8th47.5 km/h
Reverse - 1st3.2 km/h
Reverse - 2nd6.0 km/h
Reverse - 3rd8.7 km/h
Reverse - 4th13.8 km/h
Reverse - 5th25.8 km/h
Reverse - 6th37.5 km/h
hydraulic system
Circuit TypeLoad Sensing, Closed Center, PPPC
Pump TypeVariable Piston
Maximum System Pressure25500.0 kPa
Standby Pressure3600.0 kPa
Reservoir Tank Capacity24.5 L
Optional High Output Pump210.5 L/min
Pump Output Standard Pump159.1 L/min
blade range
Circle Centershift - right656.0 mm
Circle Centershift - left658.0 mm
Moldboard Sideshift - right663.0 mm
Moldboard Sideshift - left512.0 mm
Maximum Blade Position Angle90.0 Degrees
Blade Tip Range - forward40.0 Degrees
Blade Tip Range - backward5.0 Degrees
Maximum shoulder reach outside of tires - right1928.0 mm
Maximum shoulder reach outside of tires - left1764.0 mm
Maximum lift above ground410.0 mm
Maximum depth of cut775.0 mm
ripper
Ripping depth - maximum262.0 mm
Ripper shank holders, quantity5
Ripper shank holder spacing533.0 mm
Penetration force4083.0 kg
Pryout force2108.0 kg
Machine length increase, beam raised1058.0 mm
scarifier
Mid, V-Type: Working width1184.0 mm
Mid, V-Type: Scarifying depth, maximum229.0 mm
Mid, V-Type: Scarifier shank holders quantity11
Mid, V-Type: Scarifier shank holder spacing116.0 mm
gross vehicle weight maximum
Gross Vehicle Weight17000.0 kg
frame
Front-section modulus - maximum3681.0 cm3
Front-section modulus - minimum1619.0 cm3
Circle - diameter1530.0 mm
Circle - blade beam thickness30.0 mm
Drawbar - height127.0 mm
Drawbar - width76.2 mm
Front axle - height to center615.0 mm
Front axle - wheel lean, left/right18.0 Degrees
Front axle - total oscillation per side32.0 Degrees
Front-top/bottom plate - width280.0 mm
Front-top/bottom plate - thickness22.0 mm
Front-side plates - width236.0 mm
Front-side plates - thickness10.0 mm
Front-linear weights - minimum134.0 kg/m
Front-linear weights - maximum172.0 kg/m
tandems
Height438.0 mm
Width172.0 mm
Sidewall thickness - inner1.0 mm
Sidewall thickness - outer16.0 mm
Drive chain pitch44.5 mm
Wheel axle spacing1510.0 mm
Tandem oscillation - front up15.0 Degrees
Tandem oscillation - front down25.0 Degrees
service refill
Fuel Capacity305.0 L
Cooling system40.0 L
Engine Oil18.0 L
Transmission/Differential/Final Drives48.0 L
Tandem housing (each)49.0 L
Front wheel spindle bearing housing0.5 L
Circle drive housing7.0 L
dimensions
Height - ROPS Cab3326.0 mm
Height - Non-ROPS Cab3321.0 mm
Height - ROPS Canopy3326.0 mm
Ground Clearance - Center Front Axle602.0 mm
Length - Between Tandem Axles1510.0 mm
Length - Front Axle to Moldboard2598.0 mm
Length - Front Axle to Mid Tandem5870.0 mm
Length - Front Tire to Rear of Machine8265.0 mm
Length - Counterweight to Ripper9769.0 mm
Ground Clearance, Trans. Case341.0 mm
Height - Top of Cylinders2885.0 mm
Height to Exhaust Stack2865.0 mm
Width - Tire Center Lines2056.0 mm
Width - Outside Rear Tires2439.0 mm
Width - Outside Front Tires2449.0 mm
standards
ROPS/FOPSISO 3471:1994/ISO 3449:2005
SteeringISO 5010:2007
BrakesISO 3450:1996
SoundISO 6394:2008/ISO 6396:2008
BENEFITS AND FEATURES
WORK TOOLS AND ATTACHMENTS
Allows expansion of machine versatility, utilization, and performance
LEARN MORE120K STANDARD EQUIPMENT
- electrical
Alternator, 115 Ampere
Backup alarm, reversing lights
Batteries, maintenance free 750 CCA
Electrical system, 24 volt
Horn, electric
Lights, stop and tail
Motor, starting
Product Link Ready
Working lights - operator environment
Accelerator
Control console, adjustable
Gauge cluster (includes voltmeter, articulation, engine coolant temperature, air brake pressure and fuel level)
Guard rails, operator station
Hydraulic controls, load sensing (right/left blade lift, circle drive, centershift, sideshift, front wheel lean and articulation)
Indicator lights (includes high beam, LH and RH turn, low engine oil pressure, throttle lock, check engine, transmission filter bypass and check, centershift pin, brake air pressure, parking brake engaged, auto shift)
Key start/stop switch
Meter, hour
Power steering, hydraulic
Seat, vinyl-covered static
Seat belt
Steering wheel, tilt, adjustable
Storage area, cooler/lunch box
Throttle, electronic control - power train
Air cleaner, dry type radial seal with service indicator and automatic dust ejector
Air to air after cooler (ATAAC)
Blower fan
Brakes, oil disc, four-wheel air actuated
Differential with lock/unlock
Engine, Cat C7 with ACERT Technology, diesel with automatic engine derate and idle control. Meets non-current U.S. EPA Tier 2 and EU Stage II emission standards.
Fuel water separator
Muffler, under hood
Parking brake, multi-disc, sealed and oil cooled
Prescreener
Priming pump, fuel, resiliently mounted
Sediment drain, fuel tank
Tandem drive
Transmission, 8 speed forward and 6 speed reverse, power shift, direct drive with electronic shift control and overspeed protection
VHP (Variable Horse Power) - other standard equipment
Bumper, rear
CD ROM Parts Book
Circle drive slip clutch
Cutting edges, 152 mm × 16 mm (6 in × 5/8 in) curved DH-2 steel
Doors, Engine compartment
Drawbar, 4 shoe replaceable nylon composite wear strips
Endbits, 16 mm (5/8 in) DH-2 steel
Frame, articulated with safety lock
Fuel tank, 305 L (80.6 gal)
Ground level engine shutdown
Link bar, 7 position
Moldboard, 3658 mm × 610 mm × 22 mm (12 ft × 24 in × 7/8 in) blade with hydraulic sideshift and mechanical tip
S·O·S ports, engine, hydraulic, transmission and cooling
Toolbox with padlock
Vandalism protection - including cap locks for hydraulic tank, radiator access cover, fuel tank, engine and transmission oil check/fill and lockable battery boxes. - antifreeze
Extended Life Coolant to -35° C (-30° F)
120K OPTIONS
- guards
Guard, transmission - operator environment
Air conditioner with heater
Heater, cab - cabcanopy
Cab, ROPS*
Cab, Non-ROPS*
Canopy, ROPS*
Seat, vinyl adjustable
Seat, cloth, contour
Fan, defroster, front window
Fan, defroster, rear window
Sun shade, rear
Wiper/washer, rear
Wipers, intermittent front
Mirrors, dual inside
Mirrors, outside mounted
Power port, 12V accessory
Radio ready entertainment
Tachometer/Speedometer
* Weights represent changes to Typically Equipped machine weights. - power train
Autoshift - other attachments
Product Link
Snow Wing Mounting, frame-ready
AccuGrade ARO
Dryer, air
Push plate, counterweight*
Accumulator, blade lift
Battery, extreme duty (1400 CCA)
Ether, starting aid
Heater, engine coolant, 220V - hydraulics
Pump, hydraulic, high capacity (210 L/min 55.7 gal/min)
Hydraulic arrangements with one or more additional hydraulic valves are available for rear ripper, mid-mount scarifier, dozer, snow plow and snow wing. - blades moldboards
Moldboard, Deluxe: Blade, 3658 mm × 610 mm × 22 mm (12' × 24" × 7/8") with hydraulic side shift and tip and 5/8" end bits cutting edge 203 mm × 19 mm (8" × 3/4")
Blade, front
Cutting edge, 203 mm × 19 mm (8" × 3/4"). For use with 14' blade
Endbits, overlay, reversible pair for use with 203 mm (8") cutting edges
MOTEUR
Reliable performance
BENEFITS AND FEATURES
Smooth Shifting Transmission
- Full Electronic Clutch Pressure Control ensures smooth shifting and directional changes.
- Shift Torque Management helps to smooth gear changes without the use of the inching pedal, helping the operator to remain focused on the task at hand.
- Load Compensation ensures consistent shift quality regardless of blade or machine load.
- Optional Autoshift automatically shifts the transmission at optimal points for easier operation.
Oil Disc Brakes - Completely Sealed, Adjustment Free Oil-bathed, air actuated and spring-released, located at each tandem wheel to eliminate power train braking loads and to reduce service time. The large brake surface area provides dependable braking capability and extended life before rebuild.
Front Axle with Cat Live Spindle Design Cat sealed spindle keeps the bearings free from contaminants and lubricated in a lightweight oil to reduce owning and operating costs. A larger tapered roller bearing is outboard where the load is greater, extending bearing life.
Maximum power and efficiency
BENEFITS AND FEATURES
Power Management The Cat C7 engine with ACERT Technology uses electronic control, precision fuel delivery and refined air management to provide outstanding performance and lower emissions. Variable Horse Power (VHP) is standard to provide more power in the higher gears. The Electronic Throttle Control provides easier, more precise and consistent throttle operation. Engine Over-Speed Protection prevents downshifting until an acceptable safe travel speed has been established.
Balanced hydraulics deliver consistent, precise and responsive control
BENEFITS AND FEATURES
Balanced Flow, Independent Oil Supply Hydraulic flow is proportioned to ensure all implements operate simultaneously. Independent oil supply prevents cross-contamination and provides proper oil cooling, which means less heat build-up and extended component life.
Implement Control Valves Provide outstanding operator “feel” and predictable system response for unmatched implement control. To help maintain exact blade settings, lock valves are built into all control valves. Line relief valves are also incorporated into selected control valves to protect the cylinders from over pressurization.
Load-Sensing Hydraulics A load sensing variable displacement pump and advanced hydraulic valves provide superior implement control and better machine performance. Continuously matching hydraulic flow and pressure to power demands creates less heat and reduces power consumption.
Consistent and Predictable Movement The hydraulic system valves are specifically designed for each hydraulic function on the motor grader. They compensate for differences in flow requirements, based on cylinder size and the difference in surface volume between the rod end (blue) and barrel end (red) of the cylinder. The result is predictable, consistent hydraulic speeds whether extending or retracting the cylinder.
Designed for strength and durability
BENEFITS AND FEATURES
Frame Structure - Provides Consistency and Strength Front frame is a continuous top and bottom plate construction. Flanged box section design removes welds from high stress areas, improving reliability and durability. The rear frame structure has two box section channels with fully welded differential case for a solid working platform. An integrated bumper ties the rear frame together into a cohesive unit to handle high stress loads.
Drawbar, Circle and Moldboard The K Series drawbar is designed for high strength and optimum durability for any application. The circle stands up to high stress loads. Raised wear surfaces prevent circle teeth wear against the drawbar. The 64 uniformly spaced circle teeth are flame cut and heat induction hardened to resist wear, and the circle is secured to the drawbar by four support shoes for maximum support. The moldboard provides optimal curvature and large throat clearance that helps move all soil types quickly and efficiently. These features deliver excellent load distribution and minimal material buildup in the circle area while allowing large blade loads to roll freely.
Blade Lift Accumulators This optional feature uses accumulators to help absorb impact loads to the moldboard by allowing vertical blade travel. Blade lift accumulators reduce unnecessary wear and help to avoid unintended machine movement for increased operator safety.
Allows expansion of machine versatility, utilization, and performance
BENEFITS AND FEATURES
Moldboard Options Standard moldboard length is 3.7 m (12 ft). Moldboard extensions are available to increase moldboard surface area and extend reach capability.
Ground Engaging Tools A wide variety of cutting edges and end bits are available, all designed for maximum service life and productivity.
Rear Ripper/Scarifier The K Series optional ripper/scarifier is made to penetrate tough material fast and rip thoroughly for easier material movement with the moldboard. The ripper includes three shanks with the ability to add two more if needed.
Front Mounted Groups A front mounted push plate/counterweight or front blade can be ordered.
Mid-Mount Scarifier Positioned between the front axle and the circle to break up tough material that the blade can then move, all in a single pass. The V-type scarifier can accommodate up to 11 teeth.
Snow Removal Work Tools Includes snow wings, angle blades, and V-plows. Multiple mounting options are available, increasing machine versatility. (Availability may differ by region.)
Caterpillar sets the standard for comfort, convenience and visibility
BENEFITS AND FEATURES
Designed for Productivity K Series cabs are designed to keep operators comfortable, relaxed and productive. Features like low effort pedals and controls, adjustable implement controls and adjustable steering wheel angle help make work easier on the operator. A clear view to the moldboard heel and tandem tires enhance productivity and safe operation. Rocker switches and transmission shifter are backlit for night time operation.
In-dash Instrument Cluster The instrument panel, with easy-to read, high-visibility gauges and warning lamps, places vital machine information and diagnostic capability in easy view of the operator. The dash includes an engine coolant temperature gauge, an articulation gauge, voltage gauge and fuel level gauge. Service brake air pressure gauges are also standard. Speedometer and tachometer are optional. All major systems are monitored by warning lights.
Additional Cab Features Additional cab features include storage area, an adjustable control console and coat hook. Optional offerings include power port, air conditioner/heater, suspension seat, defroster fan, sun shade, backup lights, Product Link™ ready, and AccuGrade™ System ready. NOTE: Some attachments are not available in all regions.
Solutions to make work easier and more efficient
BENEFITS AND FEATURES
Cat AccuGrade AccuGrade uses positioning and guidance technologies, machine sensors, and automatic blade control to help operators get to grade faster, easier and more efficiently. Digital design plans, real-time cut/fill data, and in-cab guidance give operators detailed information to work more confidently and achieve greater accuracy, in fewer passes, using less material. Operators can stay on grade and improve productivity and accuracy by nearly 50 percent over conventional methods. Grade stakes and checkers are minimized, making the work site safe, efficient, and cost effective. AccuGrade technologies include Cross Slope, Sonic, Laser, GPS, and/or Universal Total Station (UTS).
AccuGrade Attachment Ready Option (ARO) K Series machines can be equipped with the AccuGrade ARO. It can be ordered as a factory or dealer installed option. The attachment option includes built-in mounting points and internal wiring, making installation of the AccuGrade grade control system faster and easier.
Cat Product Link Product Link helps take the guesswork out of equipment management with remote monitoring capabilities for your machine or your entire fleet. Track asset location, hours, fuel usage, diagnostic codes, idle time and more through the secure VisionLink™ user interface. Knowing where your equipment is, what it’s doing and how it’s performing enables you or your Cat dealer to manage your fleet in real-time so you can maximize efficiency, improve productivity, and lower operating costs.
Designed with safety in mind
BENEFITS AND FEATURES
ROPS/FOPS Cab Offers Low Sound and Vibration Levels The operator sound pressure level for the cab offered by Caterpillar, when properly installed, maintained and tested with the doors closed, meets or exceeds requirements set forth in ISO 6394:2008. The quiet environment helps improve operator working conditions.
Brake Systems and Machine Protection Brakes located at each tandem wheel offer the largest total brake surface area in the industry, delivering dependable stopping power and longer brake life. Standard circle drive slip clutch protects the drawbar, circle and moldboard from shock loads when the blade encounters an immovable object. Blade lift accumulators help absorb impact loads to the moldboard by allowing vertical blade travel.
Electrical Disconnect Switch and Engine Shutoff Switch Disconnect switch provides ground-level lockout of the electrical system to prevent inadvertent machine starts. Engine shutoff allows anyone nearby to shut the machine down in case of an emergency.
Additional Safety Features Laminated glass on the front windows and lockable doors to reduce theft and vandalism are available with the optional cab. Brake lights, conveniently located grab rails, back up lights and alarm also help ensure a safe work environment.
When uptime counts
BENEFITS AND FEATURES
Renowned Cat Dealer Support From helping you choose the right machine to financing and ongoing support, your Cat dealer provides the best in sales and service. Manage your costs with preventive maintenance programs like S•O•SSM fluids analysis, coolant sampling and guaranteed maintenance contracts. Stay productive with best-in-class parts availability. Your Cat dealer can help you boost your profits with operator training. And when it’s time for component replacement, your Cat dealer can help you save even more. Genuine Cat Remanufactured parts carry the same warranty and reliability as new products at savings of 40 to 70 percent for power train and hydraulic components.
Thinking generations ahead
BENEFITS AND FEATURES
- Integrated machine systems and technologies improve productivity for greater accuracy, lower fuel use and reduced machine wear.
- Replaceable wear parts save maintenance time and cost, and extend major component life.
- Ecology drains help make draining fluids more convenient and help prevent spills.
- Major components are built to be rebuilt, eliminating waste and saving customers money by giving the machine and/or major components a second - and even third life.
- A variety of safety features help safeguard operators and others on the job site.
Convenient service points make routine maintenance quick and easy
BENEFITS AND FEATURES
Grouped Service Points on the left side to help ensure proper maintenance Easy access to service areas speeds up maintenance and ensures that routine service is performed on time. Ecology drains shorten service times and help prevent spills. Radiator cleanout access gives the operator the ability to clear away debris and other materials that build up around the radiator.
Extended Service Intervals Reduce Downtime, Operating Cost
- 500 hour engine oil changes
- 4,000 hour hydraulic oil changes
- 12,000 hour engine coolant changes
Diagnostics and Machine Monitoring The dash cluster panel provides enhanced machine information and diagnostic capability, which allows faster servicing of the transmission and engine.
O-Ring Face Seals O-Ring face seals create a reliable connection and are used in all hydraulic circuits to minimize the possibility of oil leaks.
Separate Wiring Harnesses Modular harness design provides simple disconnects for major machine repairs or rebuilds which reduces machine downtime.
Cat Electronic Technician Cat Electronic Technician is a two-way communication tool that gives service technicians easy access to stored diagnostic data, reducing machine downtime and lowering operating costs.